Heat Exchangers in Petroleum Industry
Heat Exchangers in Petroleum Industry and Petrochemical Industry are critical applications used in a wide range of areas. In these industries, exchangers perform a number of important functions such as temperature control, heat transfer, energy efficiency, and inter-process temperature and pressure balancing.
Heat Exchanger Usage Areas in Petroleum and Petrochemical Industry
- Refinery Processes: In oil refineries, complex distillation and catalytic precipitation processes are used to separate crude oil into various fractions. In these processes, heat exchangers provide temperature control to control the reactions occurring at high temperatures and obtain the desired products.
- Cooling: In petroleum and petrochemical plants, many processes occur at high temperatures. Heat exchangers help cool equipment and improve product quality by controlling the heat resulting from these processes.
- Product Cooling: Petroleum products and chemicals produced in refineries or petrochemical plants must be cooled for storage and transportation processes that require temperature control. Heat exchangers are used to cool these products.
- Reactors: Temperature control is critical in reactors where chemical reactions occur. Exchangers are used to keep the temperature of reactors constant and increase reaction efficiency.
- Heat Recovery: Waste heat is generated during many processes in petroleum and petrochemical plants. Heat exchangers save energy by recovering this waste heat and reuse it in processes.
Process Intensification: In the petroleum and petrochemical industry, processes may need to be intensified to increase the efficiency of reactions. Heat exchangers provide temperature control in these condensation processes.
Washing and Separation Processes: In petroleum and petrochemical plants, heat exchangers are used to wash the products and separate their components.
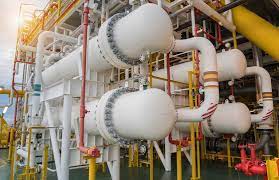
Use of Heat Exchangers in the Petroleum and Petrochemical Industry
Petroleum Applications
Petrochemical Applications
Benefits of Use of Heat Exchangers in the Petroleum and Petrochemical Industry
- Low costs by reducing the heat transfer area you need thanks to high thermal efficiency
- Low fluid operating costs due to low initial fluid requirements
- No need for complex maintenance such as X-Ray, ultrasonic and other non-destructive testing procedures in maintenance
- While the exchanger operates safely, the need for inspection and maintenance is reduced due to the corrosion-resistant material
- Reduces costs as heat exchanger life is long
- No moving parts eliminates vibration and reduces maintenance
- Reducing pollution ensures high thermal efficiency while reducing maintenance and operating costs
- Wide selection of plates and gaskets resistant to aggressive process fluids
- Ease of cleaning and installation
- Having welded and unwelded plate parts
- Reducing the possibility of leakage with limited gasket usage design
- Flexible structures to meet variable process needs
- Up to 97% heat recovery
- Efficient work
Heat Exchangers in Petroleum Industry, heat exchangers increase the efficiency of facilities, reducing energy costs, improving product quality and reducing environmental impact. Therefore, heat exchangers are widely used and critical in these industries.