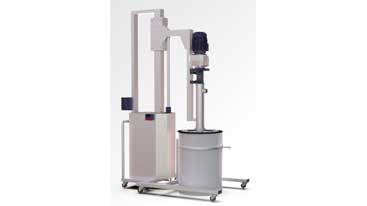
CIP Process and Industrial Cleaning: A Vital Step During Product Transfer
In industrial production facilities, accumulations, impurities and the amount of bacteria formed during product transfer can affect production quality. The CIP process (Cleaning In Place), which is used to prevent these problems and ensure the hygiene of the facilities, stands out especially with the Sesinoks design and CIP unit equipment.
What is CIP Process and How is It Applied?
Cleaning In Place (CIP) is a cleaning process used to clean the accumulations that occur on the line during product transfer and reduce the amount of bacteria. In this application, a water-acid mixture is prepared at a concentration determined according to the type of product passing through the line. This prepared and heated liquid is pressed into the line through specially designed pump systems and the washing process is carried out. These systems can be specially designed according to the capacity and needs of the facility and can be designed manually or automatically.